Autobehavior Rig
One of the main projects I have worked on in my college career is the Autobehavior Rig. I worked on this project for Goard Laboratory at UCSB. The purpose of this device is to allow mice to play simple video games. Goard Laboratory is currently using five of these rigs to gain valuable data about cognitive behavior.
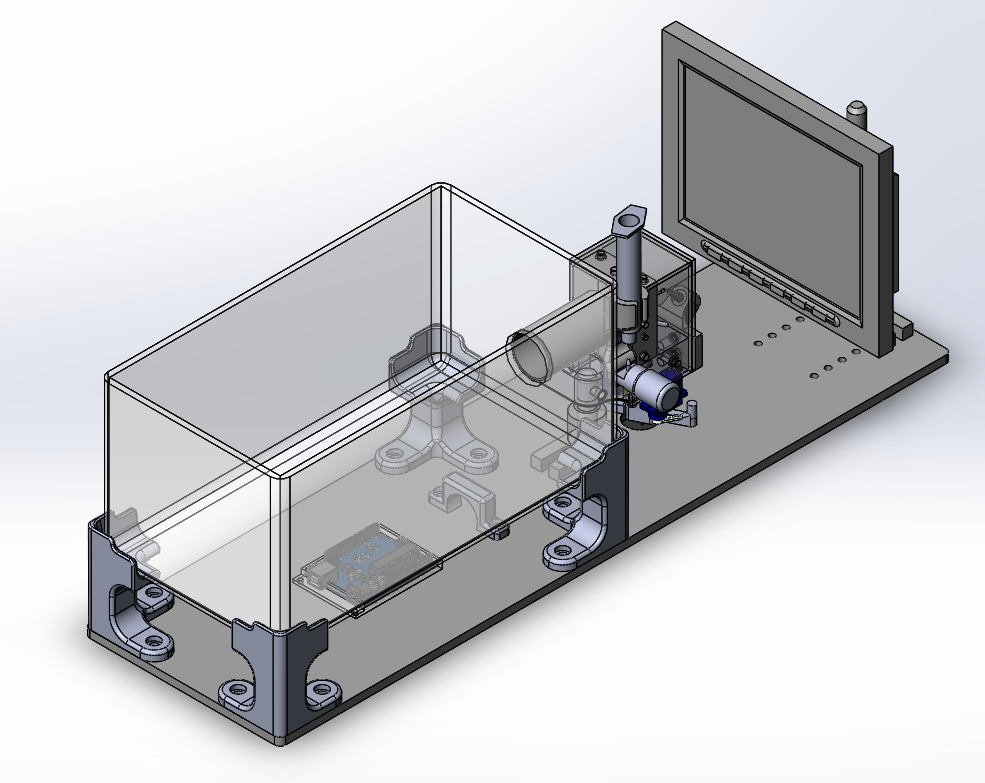
This project involved designing custom parts to be 3D printed, making a custom PCB (printed circuit board), and extensive CAD modelling in Solidworks. The figure above depicts a CAD model of the autobehavior rig.
The front compartment of the Rig is where the mice plays the video games. The rules of the game are simple, the mouse must move a ball either left or right to hit a target. If the mouse moves the ball in the correct direction it scores a point. The mouse controls a virtual ball on the screen with a joystick. The angular position of the joystick is measured with an optical encoder. This optical encoder is connected to the PCB allowing it to transmit the information of the joystick angular position to the PCB. When the mouse scores a point it is rewarded with water. A solenoid valve controls the mouse water supply and is actuated when the mouse scores a point.
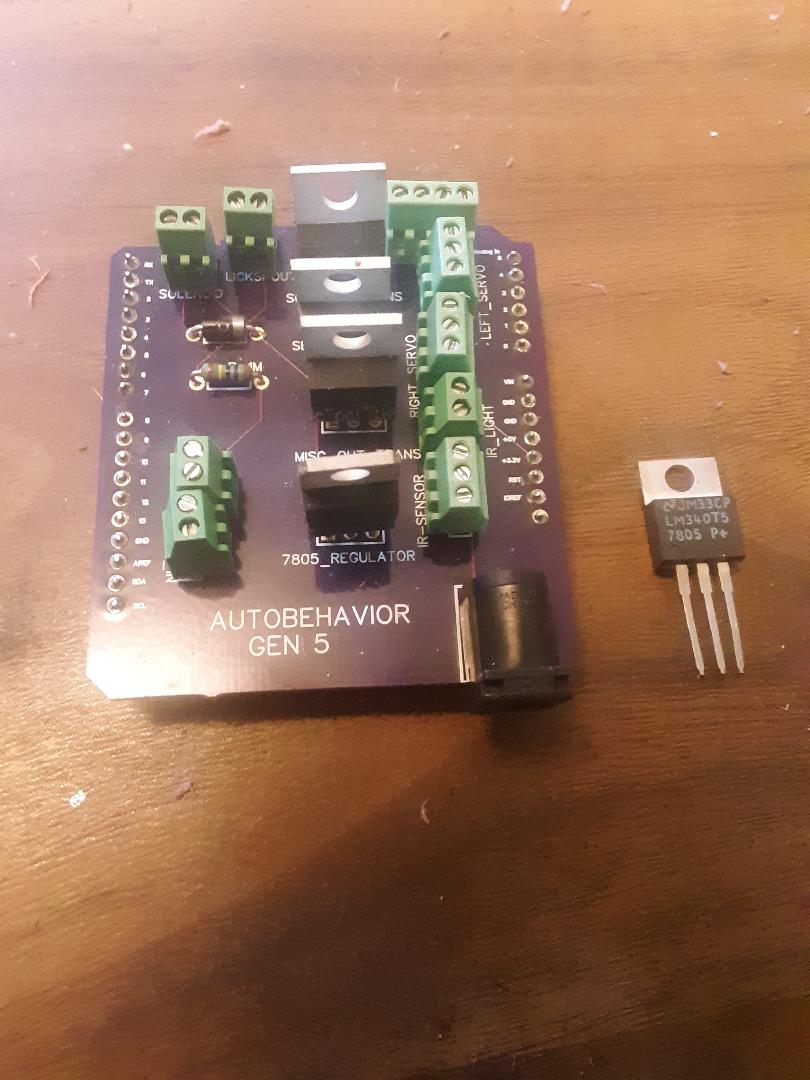
The Rig is turned off when the mouse is in its cage. When the mouse travels through the aluminum tube connecting the cage and the front compartment of the Rig it triggers an IR sensor. When the sensor detects the mouse the entire rig turns on. This means that the screen in front of the Rig turns on so the mouse can play the game. Furthermore, servos move to allow the mouse to turn the joystick. When the Rig is turned off the servos lock the joystick in place.
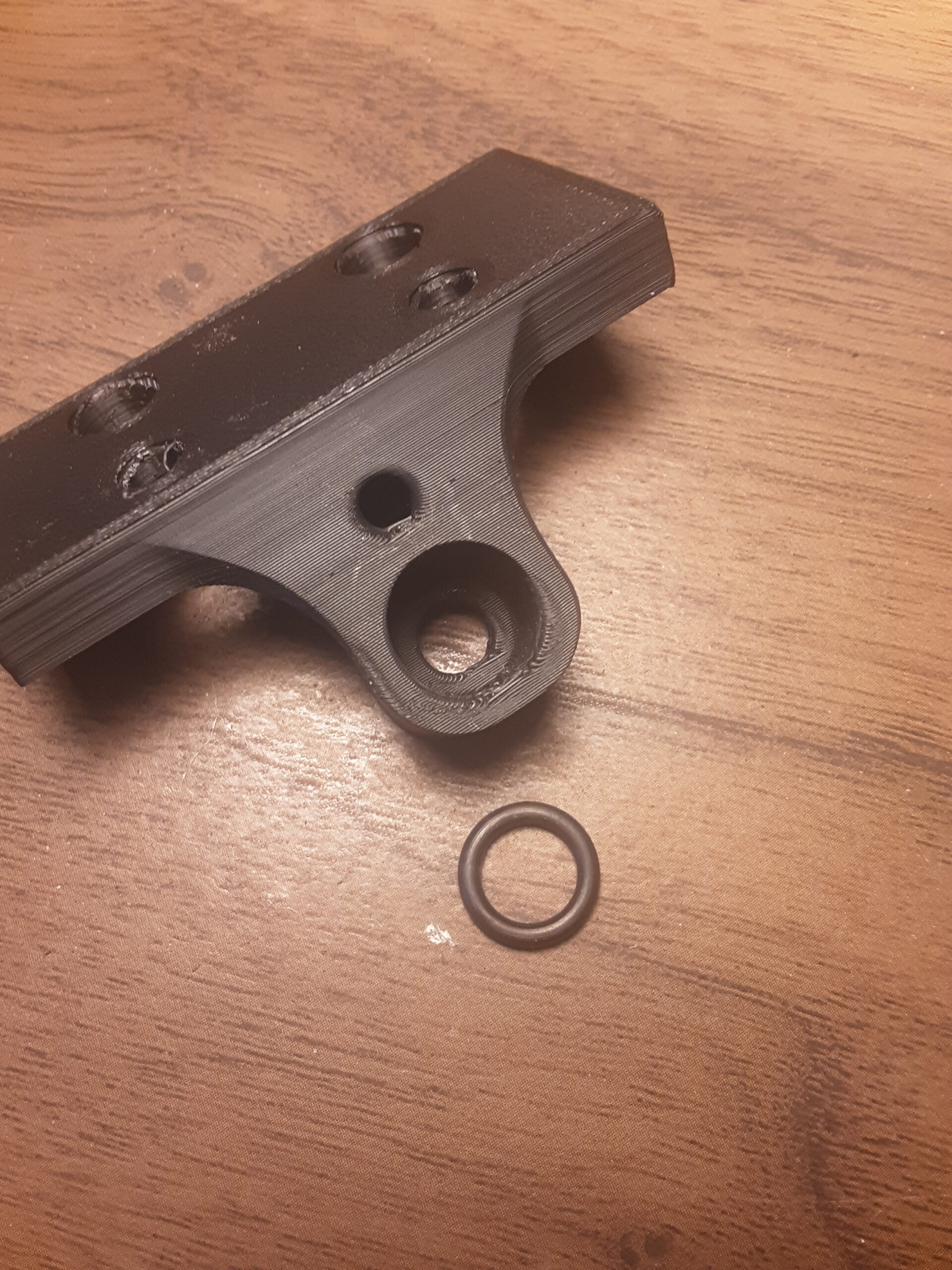
The autobehavior rig has five custom 3D printed parts. These parts are the lickspount mount, the back panel, the bottom panel, the cage mounts and the joystick attachment. These parts were all designed using Solidworks before they were printed. Designing these parts required multiple iterations as many of the holes for screws and threaded inserts had tight tolerances.
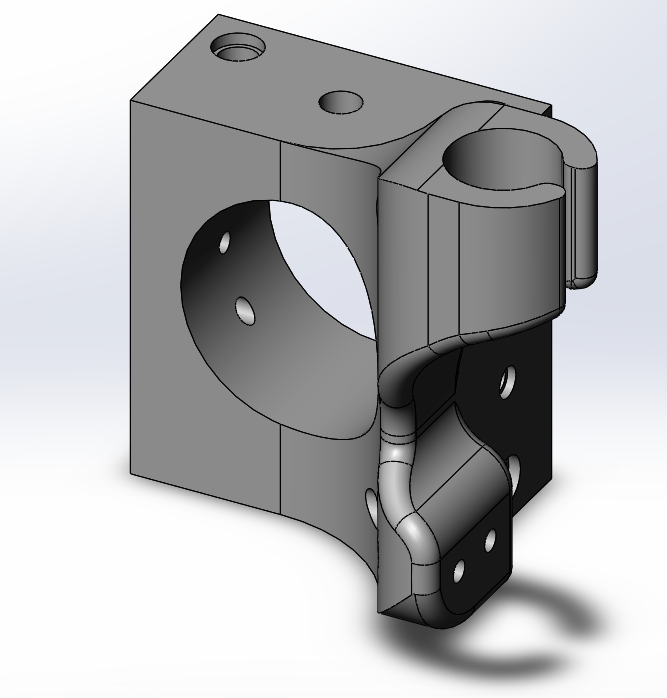
Back Panel
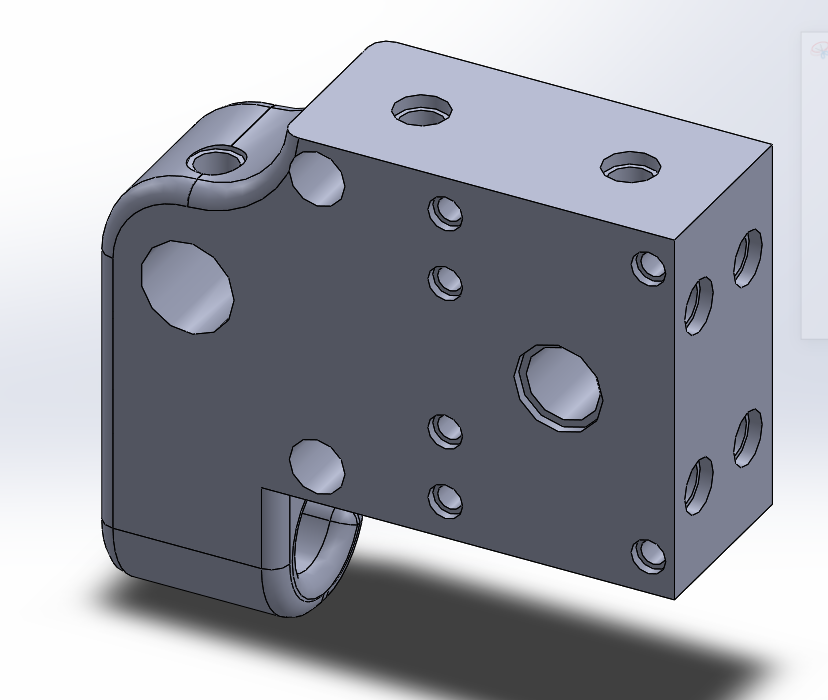
Bottom Panel
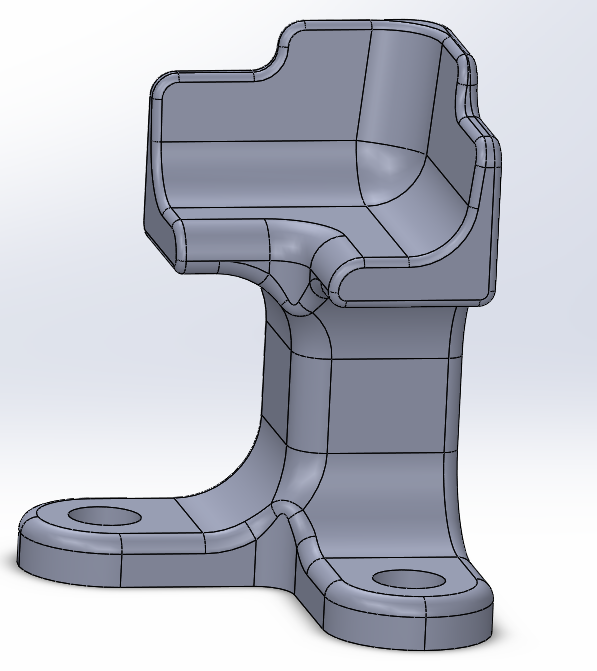
Cage Mount
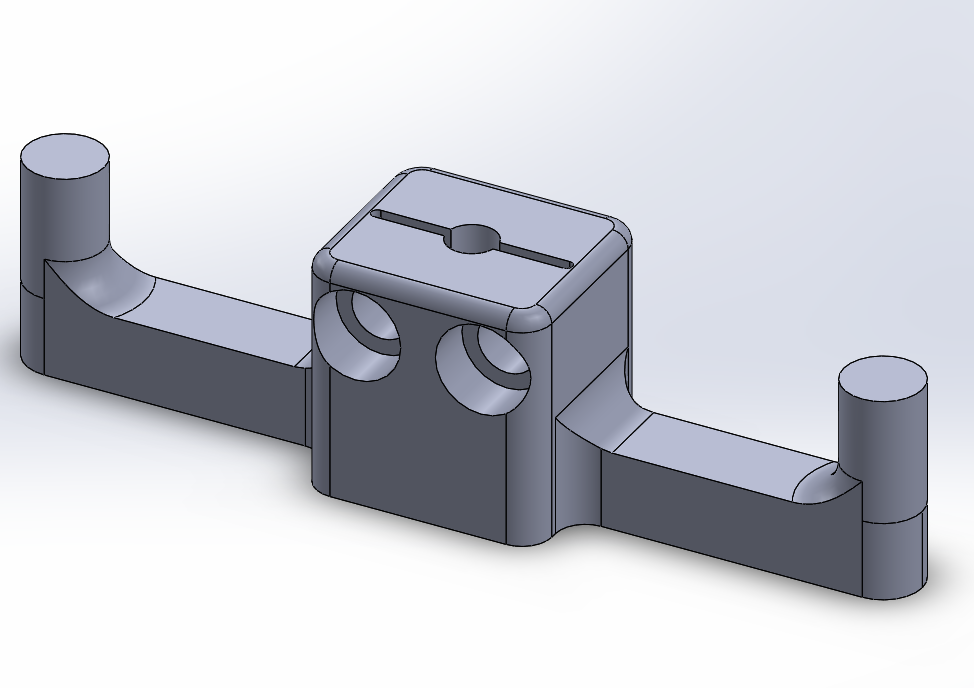
Joystick Attachment
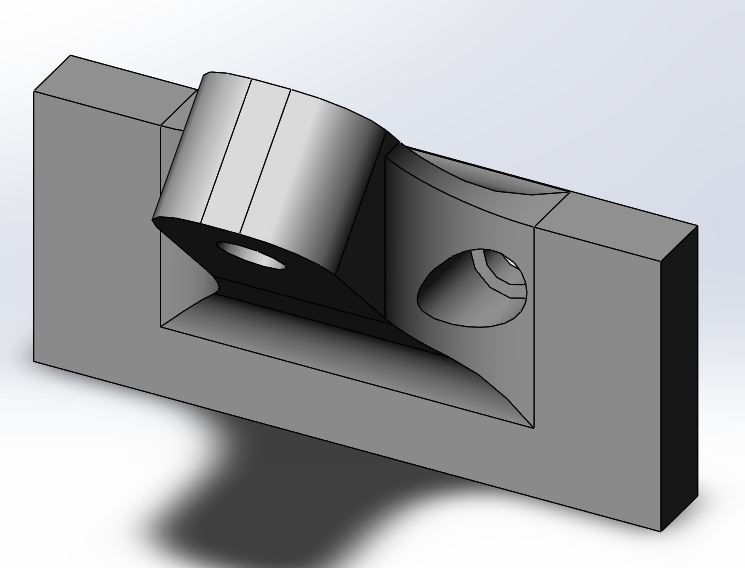
Lickspout Mount
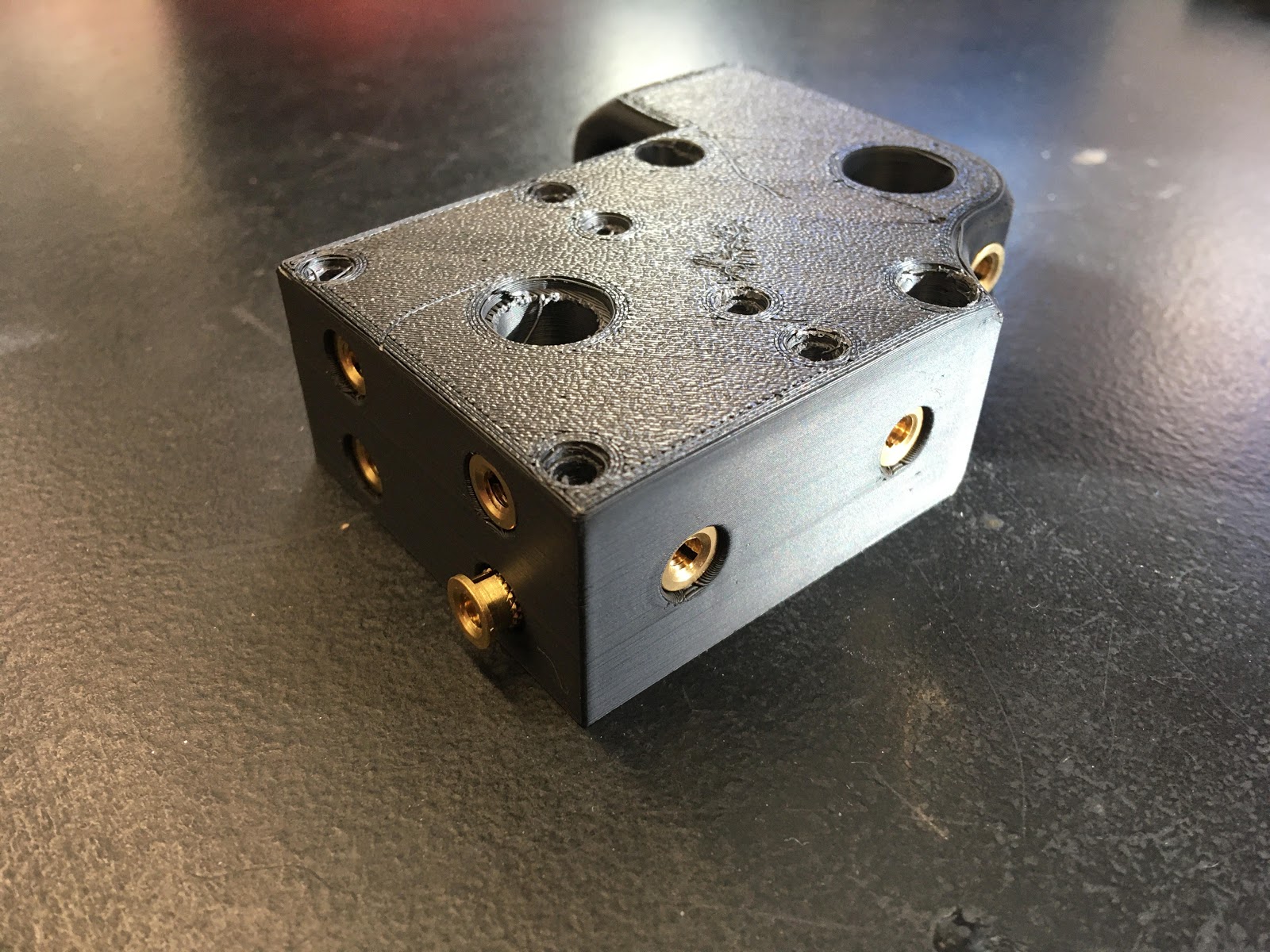
The bottom panel is the base of the front compartment of the autobehavior rig. The front compartment is where the mouse plays the video game. The large hole in the center of the panel is where the ball bearing is placed. The diameter of the bearing hole is slightly larger than the diameter of the bearing so that the ball bearing fits snuggly into the hole. The joystick is then put through the center of the bearing allowing the joystick to rotate. The other holes on bottom of the panel are for attaching other components like the servos or optical encoder. Threaded inserts are placed in the holes so that components can be screwed into the bottom panel. An optical post is used to mount the bottom panel above the ground so it is level with the cage making it easy for the mouse to travel between the cage and the front compartment. The side and front panels are also attached via the threaded inserts to sides of the bottom panels.